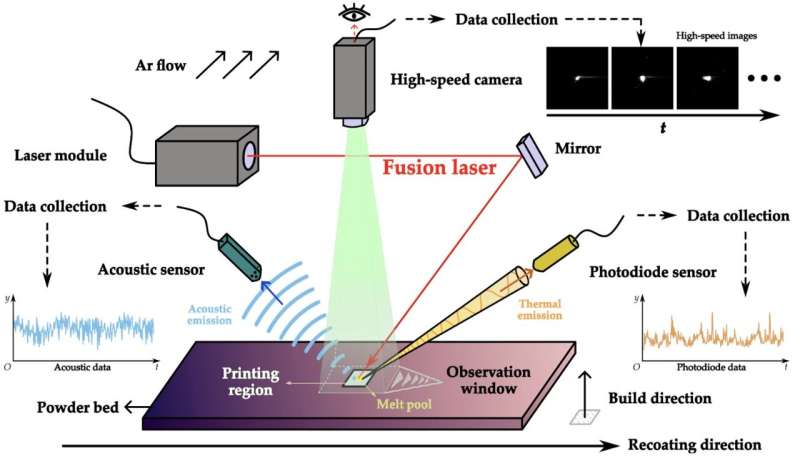
Many things can go wrong when additively manufacturing (AM) metal and without in-situ process monitoring, defects can only be detected and characterized after a product is built. Most commonly, manufacturers will use a high-speed camera to keep an eye on the melt pool geometry and its variation during a short period of the laser powder bed fusion (LPBF) process.
This requires an expensive piece of equipment, extensive memory storage—i.e. saving 20 to 30 thousand high-resolution photos each second—and laborious human efforts to collect and categorize the data. These eventually elevate the cost of online visual tracking and process analysis.
To achieve automatic, cost-efficient in-situ visual monitoring during metal AM, researchers in Carnegie Mellon University’s College of Engineering have developed a deep-learning approach that offers an alternative way to capture and characterize melt pools in LBPF using merely airborne acoustic or thermal emissions.
The team’s method, recently published in the Journal of Additive Manufacturing, enables manufacturers to acquire essential melt pool geometries and predict transient melt pool variabilities almost instantaneously.
“By leveraging the underlying physics of multi-modal process signals and the advantages of data-driven artificial intelligence, our pipeline enables engineers to reconstruct critical melt pool characteristics using very affordable and accessible sensors such as microphones or photodiodes,” said Haolin Liu, Ph.D. candidate in Mechanical Engineering.
One clear benefit of this new approach is its potential ability to identify spatially dependent lack-of-fusion (LOF) defects in LPBF. As one of the most typical process anomalies, LOF occurs when there is insufficient melt pool overlap as the laser works its way across the powder layer.
The resultant unmelted powder leaves the part with huge unfused gaps and residual pores that could severely undermine the durability and other mechanical properties of the final product. Therefore, capturing these local flaws as well as melt pool variations in real-time is critical to manufacturing consistently durable products.
The team conducted a series of LPBF experiments to explore various printing parameters of the titanium alloy, Ti-6Al-4V (Ti-64). Airborne acoustic, thermal, and high-speed imaging data was collected and synchronized for each corresponding process condition from a pre-designed, as-built structure to successfully reconstruct accurate melt pool geometries. The team even tracked the melt pool oscillational behaviors over a period as short as only a few milliseconds. The approach also exhibited promising capabilities to effectively detect local LOF defects between two adjacent laser scanlines.
“This method is allowing melt pool monitoring using low-cost sensors that can be installed in any laser powder bed AM machine. The generation of artificial videos of high-speed melt pools from acoustic and photodiode sensor data is unique to the AM community,” said Jack Beuth, mechanical engineering professor and co-director of NextManufacturing Center.
Moreover, the team’s research has also resulted in a crucial step toward better understanding the physical correlation between multi-modal in-situ process signals.
“The intercorrelations between these signals have not yet been fully explored in the scientific community,” said Liu.
“Though our research was focused on a deep learning, data-driven pipeline, we revealed that certain rudimental connections exist between acoustic signatures, thermal emissions, and melt pool morphologies, the physics and dynamics of which require further scientific exploration and experimental investigation.”
“Although many experts have been aware of the interplay between acoustic emissions, thermal emissions, and the resulting melt pool dynamics in laser printing, the precise relationships are still largely unknown,” said Levent Burak Kara, mechanical engineering professor.
“In this work, we established and demonstrated a data-driven predictive model that relates these three phenomena in a quite accurate and physically meaningful way.”
According to Anthony Rollett, materials science and engineering professor and co-director of the NextManufacturing Center, acoustic behaviors entail essential physical interactions between laser and materials.
“To our surprise, it reveals more than we had expected and it turns out to be very useful for informing process-related quantities that could potentially impact manufacturing quality.”
Moving forward, the team plans to explore more real-time monitoring applications driven by acoustic and thermal emission data for materials other than Ti-64 and across different platforms and AM processes.
“With a deeper interpretation of potentials of acoustic and thermal emission, we hope to better understand their relationships to melt pool variability, keyhole oscillation, and other spatially dependent process features,” said Liu.
“One day, we may build advanced surrogate models and fully functional digital twins for other process characterization equipment like synchrotron X-ray machines and the entire AM process too!”
More information:
Haolin Liu et al, Inference of highly time-resolved melt pool visual characteristics and spatially-dependent lack-of-fusion defects in laser powder bed fusion using acoustic and thermal emission data, Additive Manufacturing (2024). DOI: 10.1016/j.addma.2024.104057
Carnegie Mellon University Mechanical Engineering
Researchers develop deep learning alternative to monitoring laser powder bed fusion (2024, April 24)
retrieved 25 April 2024
from https://techxplore.com/news/2024-04-deep-alternative-laser-powder-bed.html
part may be reproduced without the written permission. The content is provided for information purposes only.
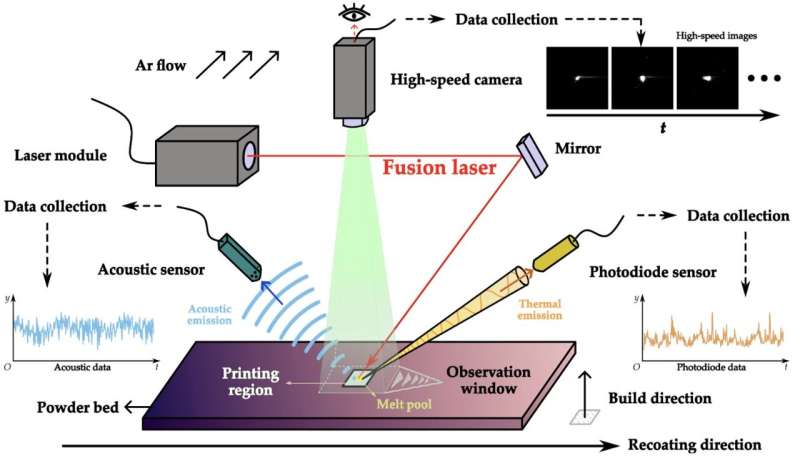
Many things can go wrong when additively manufacturing (AM) metal and without in-situ process monitoring, defects can only be detected and characterized after a product is built. Most commonly, manufacturers will use a high-speed camera to keep an eye on the melt pool geometry and its variation during a short period of the laser powder bed fusion (LPBF) process.
This requires an expensive piece of equipment, extensive memory storage—i.e. saving 20 to 30 thousand high-resolution photos each second—and laborious human efforts to collect and categorize the data. These eventually elevate the cost of online visual tracking and process analysis.
To achieve automatic, cost-efficient in-situ visual monitoring during metal AM, researchers in Carnegie Mellon University’s College of Engineering have developed a deep-learning approach that offers an alternative way to capture and characterize melt pools in LBPF using merely airborne acoustic or thermal emissions.
The team’s method, recently published in the Journal of Additive Manufacturing, enables manufacturers to acquire essential melt pool geometries and predict transient melt pool variabilities almost instantaneously.
“By leveraging the underlying physics of multi-modal process signals and the advantages of data-driven artificial intelligence, our pipeline enables engineers to reconstruct critical melt pool characteristics using very affordable and accessible sensors such as microphones or photodiodes,” said Haolin Liu, Ph.D. candidate in Mechanical Engineering.
One clear benefit of this new approach is its potential ability to identify spatially dependent lack-of-fusion (LOF) defects in LPBF. As one of the most typical process anomalies, LOF occurs when there is insufficient melt pool overlap as the laser works its way across the powder layer.
The resultant unmelted powder leaves the part with huge unfused gaps and residual pores that could severely undermine the durability and other mechanical properties of the final product. Therefore, capturing these local flaws as well as melt pool variations in real-time is critical to manufacturing consistently durable products.
The team conducted a series of LPBF experiments to explore various printing parameters of the titanium alloy, Ti-6Al-4V (Ti-64). Airborne acoustic, thermal, and high-speed imaging data was collected and synchronized for each corresponding process condition from a pre-designed, as-built structure to successfully reconstruct accurate melt pool geometries. The team even tracked the melt pool oscillational behaviors over a period as short as only a few milliseconds. The approach also exhibited promising capabilities to effectively detect local LOF defects between two adjacent laser scanlines.
“This method is allowing melt pool monitoring using low-cost sensors that can be installed in any laser powder bed AM machine. The generation of artificial videos of high-speed melt pools from acoustic and photodiode sensor data is unique to the AM community,” said Jack Beuth, mechanical engineering professor and co-director of NextManufacturing Center.
Moreover, the team’s research has also resulted in a crucial step toward better understanding the physical correlation between multi-modal in-situ process signals.
“The intercorrelations between these signals have not yet been fully explored in the scientific community,” said Liu.
“Though our research was focused on a deep learning, data-driven pipeline, we revealed that certain rudimental connections exist between acoustic signatures, thermal emissions, and melt pool morphologies, the physics and dynamics of which require further scientific exploration and experimental investigation.”
“Although many experts have been aware of the interplay between acoustic emissions, thermal emissions, and the resulting melt pool dynamics in laser printing, the precise relationships are still largely unknown,” said Levent Burak Kara, mechanical engineering professor.
“In this work, we established and demonstrated a data-driven predictive model that relates these three phenomena in a quite accurate and physically meaningful way.”
According to Anthony Rollett, materials science and engineering professor and co-director of the NextManufacturing Center, acoustic behaviors entail essential physical interactions between laser and materials.
“To our surprise, it reveals more than we had expected and it turns out to be very useful for informing process-related quantities that could potentially impact manufacturing quality.”
Moving forward, the team plans to explore more real-time monitoring applications driven by acoustic and thermal emission data for materials other than Ti-64 and across different platforms and AM processes.
“With a deeper interpretation of potentials of acoustic and thermal emission, we hope to better understand their relationships to melt pool variability, keyhole oscillation, and other spatially dependent process features,” said Liu.
“One day, we may build advanced surrogate models and fully functional digital twins for other process characterization equipment like synchrotron X-ray machines and the entire AM process too!”
More information:
Haolin Liu et al, Inference of highly time-resolved melt pool visual characteristics and spatially-dependent lack-of-fusion defects in laser powder bed fusion using acoustic and thermal emission data, Additive Manufacturing (2024). DOI: 10.1016/j.addma.2024.104057
Carnegie Mellon University Mechanical Engineering
Researchers develop deep learning alternative to monitoring laser powder bed fusion (2024, April 24)
retrieved 25 April 2024
from https://techxplore.com/news/2024-04-deep-alternative-laser-powder-bed.html
part may be reproduced without the written permission. The content is provided for information purposes only.