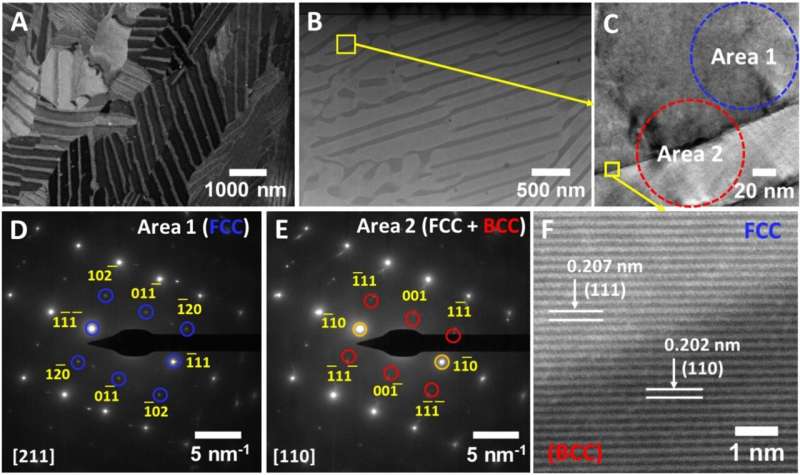
What makes structures and materials designed for extreme environments reliable? Research led by the University of Alabama at Birmingham and published in Scientific Reports details developments in the understanding of additively manufactured materials under high pressures through the use of high-resolution imaging and computer simulations.
Yogesh Vohra, Ph.D., professor in the Department of Physics and associate dean for Research and Innovation in the College of Arts and Sciences, serves as the principal investigator for the Center for Additively Manufactured Complex Systems under Extremes.
To produce better materials for human use in extreme environments, CAMCSE studies how 3D-printed materials perform under extremes of pressures, temperatures, and high-velocity impact or shock compression.
Using focused ion beam technology to extract a compressed sample a few nanometers thick, the electron microscopy observations confirmed the irreversibility of the phase transformation. The nano-layer arrangement remained undisturbed even after exposure to extreme pressures.
Vohra says the published research focuses on the fundamental structural reasons behind the high strength and ductility of 3D-printed alloys.
“In particular, how crystal structure changes under high pressures might impact the mechanical properties of 3D-printed alloys,” Vohra said.
“The electron microscopy study in this paper is significant as it established for the first time that the nanostructured layered structure is maintained after exposure to pressure and there is no change in chemical composition of individual layers.”
This research will allow for developments in the design of additively manufactured materials for extreme high temperatures in aerospace and power plant applications, resilient structures under hypervelocity impacts, and high-radiation environments in nuclear reactors.
Vohra says he is excited about this development in CAMCSE as it represents advancement in the understanding of crystal structure changes induced by high pressure and highlights the significance of collaboration.
“This paper represents collective expertise of four different academic institutions applied to 3D-printed super alloys under extremes,” Vohra said.
“Working across science and engineering disciplines on a common problem is a notable achievement of CAMCSE and at the same time provides training opportunities to UAB graduate students.”
More information:
Andrew D. Pope et al, High-pressure phase transition in 3-D printed nanolamellar high-entropy alloy by imaging and simulation insights, Scientific Reports (2024). DOI: 10.1038/s41598-024-67422-x
University of Alabama at Birmingham
Researchers test stability of 3D-printed super alloy under extremes (2024, August 27)
retrieved 27 August 2024
from https://techxplore.com/news/2024-08-stability-3d-super-alloy-extremes.html
part may be reproduced without the written permission. The content is provided for information purposes only.
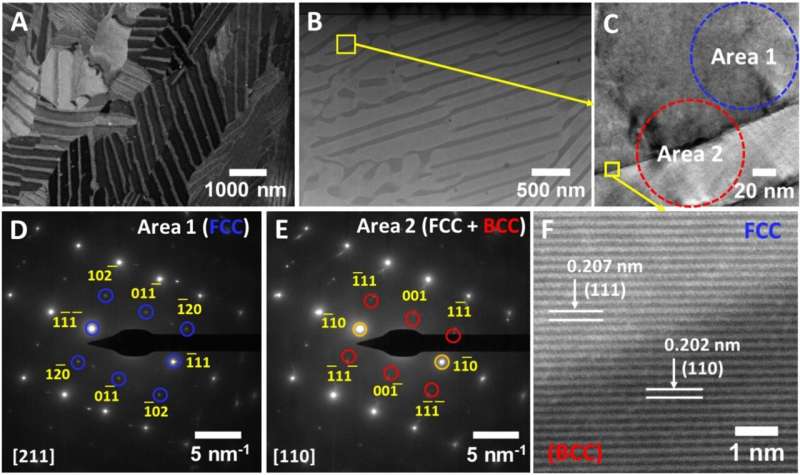
What makes structures and materials designed for extreme environments reliable? Research led by the University of Alabama at Birmingham and published in Scientific Reports details developments in the understanding of additively manufactured materials under high pressures through the use of high-resolution imaging and computer simulations.
Yogesh Vohra, Ph.D., professor in the Department of Physics and associate dean for Research and Innovation in the College of Arts and Sciences, serves as the principal investigator for the Center for Additively Manufactured Complex Systems under Extremes.
To produce better materials for human use in extreme environments, CAMCSE studies how 3D-printed materials perform under extremes of pressures, temperatures, and high-velocity impact or shock compression.
Using focused ion beam technology to extract a compressed sample a few nanometers thick, the electron microscopy observations confirmed the irreversibility of the phase transformation. The nano-layer arrangement remained undisturbed even after exposure to extreme pressures.
Vohra says the published research focuses on the fundamental structural reasons behind the high strength and ductility of 3D-printed alloys.
“In particular, how crystal structure changes under high pressures might impact the mechanical properties of 3D-printed alloys,” Vohra said.
“The electron microscopy study in this paper is significant as it established for the first time that the nanostructured layered structure is maintained after exposure to pressure and there is no change in chemical composition of individual layers.”
This research will allow for developments in the design of additively manufactured materials for extreme high temperatures in aerospace and power plant applications, resilient structures under hypervelocity impacts, and high-radiation environments in nuclear reactors.
Vohra says he is excited about this development in CAMCSE as it represents advancement in the understanding of crystal structure changes induced by high pressure and highlights the significance of collaboration.
“This paper represents collective expertise of four different academic institutions applied to 3D-printed super alloys under extremes,” Vohra said.
“Working across science and engineering disciplines on a common problem is a notable achievement of CAMCSE and at the same time provides training opportunities to UAB graduate students.”
More information:
Andrew D. Pope et al, High-pressure phase transition in 3-D printed nanolamellar high-entropy alloy by imaging and simulation insights, Scientific Reports (2024). DOI: 10.1038/s41598-024-67422-x
University of Alabama at Birmingham
Researchers test stability of 3D-printed super alloy under extremes (2024, August 27)
retrieved 27 August 2024
from https://techxplore.com/news/2024-08-stability-3d-super-alloy-extremes.html
part may be reproduced without the written permission. The content is provided for information purposes only.